Encoders and sensors for your specific machine and system
Production uptime and precision are critical factors in the complex production processes of the pulp and paper industry. Leine Linde’s encoders and sensors provide reliable feedback on position and speed throughout the papermaking process so that all drives and motors can work smoothly and with precise control.
Leine Linde encoders can be trusted to deliver precise data, month after month and year after year - even in demanding environments. We have an excellent track record in the pulp & paper industry. By using our products, you minimize the risk of costly and time-consuming downtime. Suitable products are presented below.
Contact your nearest Leine Linde office for further consultation on the best product choice for your specific machines and system.
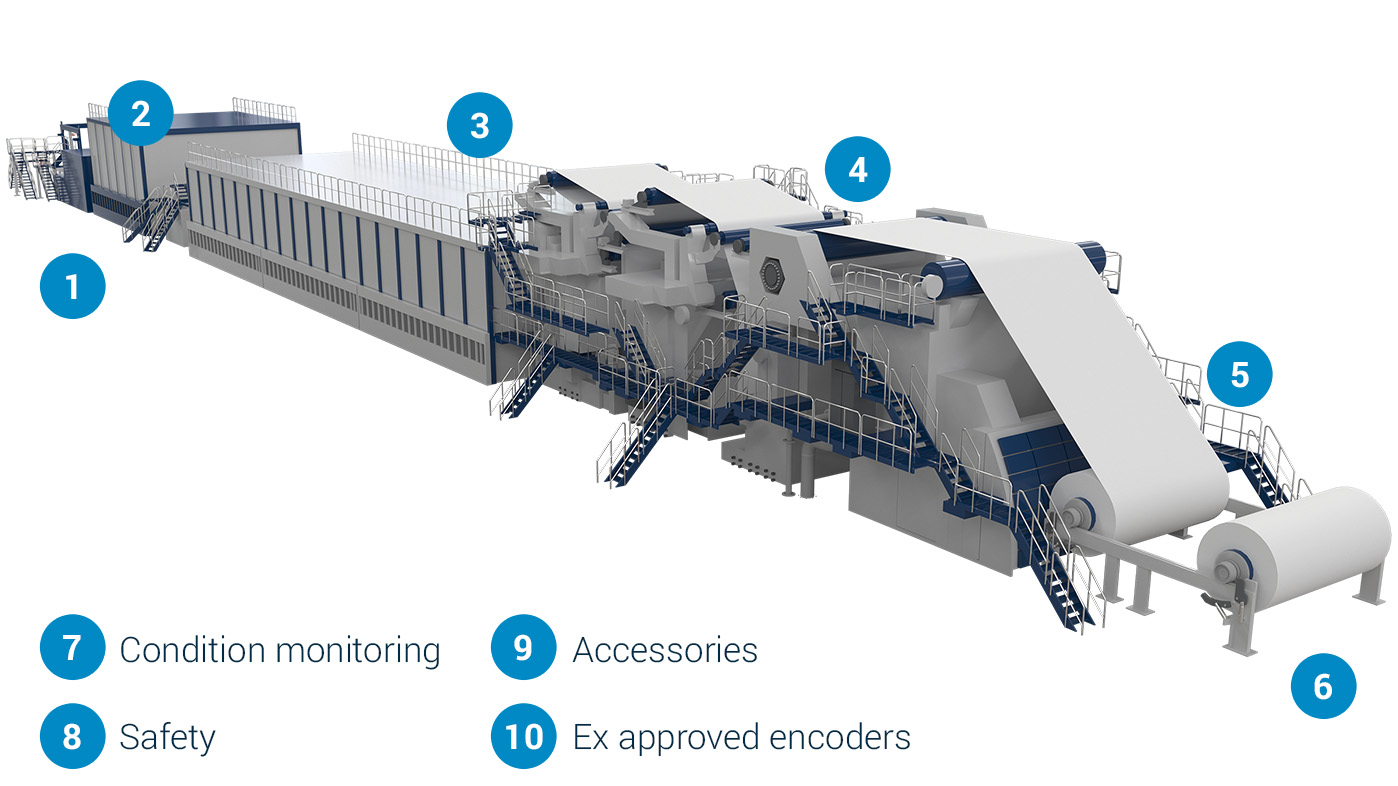
Pulping & wet end
The pulp-making operating conditions are wet, humid, and can vary a great deal in temperature. Robust and durable machine components are necessary, and when you need precision, the encoders from Leine Linde do their job perfectly. Get absolute position feedback for automated processes or control the opening of the pulp distributor by incremental encoders measuring speed and number of turns of the opening screw. Ensure a smooth conveyor and feeding system as well as equal quantities of pulp for uniform bales.
Wet press section
Throughout the Fourdrinier process where excess water is eliminated, it is of utmost urgency to ensure the stability and smoothness in operation of the motors for perfect wire speed. Getting precise and high-resolution information from the encoders is essential for process control. Vibrations, heat, and chemicals are part of the process, which reliable encoders can withstand.
Dryer section
The conditions in the dryer section can be very hot and humid, both from the paper product and from the steam used to heat the drying cylinders. The speed of the rollers and cylinders must slow down progressively by each drying section, because the paper will shrink as it dries. Leine Linde encoders supply the feedback needed for precise control in the dryer section.
Finishing section
The paper passes through a calender where steel cylinders at a precisely determined width apart ensure that the paper thickness is consistently even. Coating is sometimes a part of the process in the finishing section.
In the finishing section the system has to handle heavy weight, shock, vibrations and strain in a dusty environment. The speed of rolls, drums and reels must be controlled in a very exact manner, in a demanding environment. This is where the industrial and heavy-duty Leine Linde encoders excel by providing precise and reliable feedback with a minimum of required maintenance.
Winding and cutting section
When the paper is formed and all the parameters are defined, then the sheet is wound onto a series of steel cores, which press against a pope reel. This make sure that the paper is wound at the right tension onto each core.
Frequently, the paper line creates a jumbo reel containing kilometers of length of paper sheet with a precise width and weight. Then the paper is switched from one reel to the next one which requires a cross-cutting process where absolute position and speed monitoring is needed.
If a certain width is required, this can also mean extra cutting and rewinding.
Sheet cutting or packaging
After winding and cutting, the finished paper rolls are moved to sheet cutting or to the packaging station for wrapping and packaging that will protect from damage during transport and storage. Encoders with built-in functional safety are especially useful in operations that involve moving or handling heavy paper rolls.
Secure your uptime with encoder diagnostics
Encoders with condition monitoring functionalities, enable predictive maintenance for problem-free operation. They can also provide relevant information about potential sources of failure, which otherwise would risk affecting the production unit as a whole.
Functional safety using encoder relay output
Implement functional safety compliant with the European Machinery Directive with encoder safety relays connected directly to the emergency stop loop or directly to selected braking functions.
Gateways that simplify system integration
Our encoders and gateways are available with a wide range fieldbus interfaces and communication protocols, making them easy to integrate in your process control system.
Ex approved encoders
In potentially explosive atmospheres, for example when chemicals and paints with sensitive substances are involved, use an ATEX or IECEx rated encoder for zones 1/21, available as both absolute and incremental encoders.